Registration Dossier
Registration Dossier
Data platform availability banner - registered substances factsheets
Please be aware that this old REACH registration data factsheet is no longer maintained; it remains frozen as of 19th May 2023.
The new ECHA CHEM database has been released by ECHA, and it now contains all REACH registration data. There are more details on the transition of ECHA's published data to ECHA CHEM here.
Diss Factsheets
Use of this information is subject to copyright laws and may require the permission of the owner of the information, as described in the ECHA Legal Notice.
EC number: 266-970-4 | CAS number: 67711-94-8 Mainly copper, copper oxides, some oxides of lead and minor metals, skimmed from the anode furnace and returned to the converter.
- Life Cycle description
- Uses advised against
- Endpoint summary
- Appearance / physical state / colour
- Melting point / freezing point
- Boiling point
- Density
- Particle size distribution (Granulometry)
- Vapour pressure
- Partition coefficient
- Water solubility
- Solubility in organic solvents / fat solubility
- Surface tension
- Flash point
- Auto flammability
- Flammability
- Explosiveness
- Oxidising properties
- Oxidation reduction potential
- Stability in organic solvents and identity of relevant degradation products
- Storage stability and reactivity towards container material
- Stability: thermal, sunlight, metals
- pH
- Dissociation constant
- Viscosity
- Additional physico-chemical information
- Additional physico-chemical properties of nanomaterials
- Nanomaterial agglomeration / aggregation
- Nanomaterial crystalline phase
- Nanomaterial crystallite and grain size
- Nanomaterial aspect ratio / shape
- Nanomaterial specific surface area
- Nanomaterial Zeta potential
- Nanomaterial surface chemistry
- Nanomaterial dustiness
- Nanomaterial porosity
- Nanomaterial pour density
- Nanomaterial photocatalytic activity
- Nanomaterial radical formation potential
- Nanomaterial catalytic activity
- Endpoint summary
- Stability
- Biodegradation
- Bioaccumulation
- Transport and distribution
- Environmental data
- Additional information on environmental fate and behaviour
- Ecotoxicological Summary
- Aquatic toxicity
- Endpoint summary
- Short-term toxicity to fish
- Long-term toxicity to fish
- Short-term toxicity to aquatic invertebrates
- Long-term toxicity to aquatic invertebrates
- Toxicity to aquatic algae and cyanobacteria
- Toxicity to aquatic plants other than algae
- Toxicity to microorganisms
- Endocrine disrupter testing in aquatic vertebrates – in vivo
- Toxicity to other aquatic organisms
- Sediment toxicity
- Terrestrial toxicity
- Biological effects monitoring
- Biotransformation and kinetics
- Additional ecotoxological information
- Toxicological Summary
- Toxicokinetics, metabolism and distribution
- Acute Toxicity
- Irritation / corrosion
- Sensitisation
- Repeated dose toxicity
- Genetic toxicity
- Carcinogenicity
- Toxicity to reproduction
- Specific investigations
- Exposure related observations in humans
- Toxic effects on livestock and pets
- Additional toxicological data
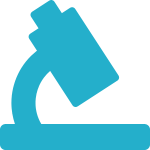
Additional physico-chemical information
Administrative data
- Endpoint:
- other: representative mineralogy
- Type of information:
- experimental study
- Adequacy of study:
- key study
- Reliability:
- 2 (reliable with restrictions)
- Rationale for reliability incl. deficiencies:
- other: No GLP study but other quality assurance
Cross-referenceopen allclose all
- Reason / purpose for cross-reference:
- reference to same study
- Reason / purpose for cross-reference:
- reference to other study
Data source
Reference
- Reference Type:
- study report
- Title:
- Unnamed
- Year:
- 2 010
Materials and methods
- Principles of method if other than guideline:
- Chemistry /elemental analysis was determined using ICP (inductively Coupled Plasma spectroscopy). Metal speciation/metal mineralogy was assessed from Sequential extraction/metal analysis and mineralogical analysis (XRD and microscopes equipped with EDS (Energy Dispersive Spectrometry) and WDS (Wavelength Dispersive Spectrometry) analysers. The interpretation of the overall results was performed by expert (with profound knowledge of metal particularities).
- GLP compliance:
- no
- Remarks:
- but equivalent Quality Assurance
Test material
- Reference substance name:
- Slags, copper refining
- EC Number:
- 266-970-4
- EC Name:
- Slags, copper refining
- Cas Number:
- 67711-94-8
- Molecular formula:
- The substance is a UVCB for which it is not possible to provide a molecular formula and a molecular weight.
- IUPAC Name:
- slag, copper refining
- Details on test material:
- Sample collection made according to ECI/REACH Copper Consortium Standards Protocols (see IUCLID section 1.4 and 4.1 attachment)
Sample Description Sample Code Lab code
B8 copper-rich slag from Secondary smelter MC_B8_531_xxx_0904 09TT03335
B8 Cu-rich slag, from slag concentrator, primary smelter (representative, homogenized) slag concentrate 09TT03987
B8 Cu-rich slag from FSF, primary smelter (representative, homogenized) slag from FSF, primary smelter 09TT05248
B8 Cu-rich slag from anode furnace, primary smelter (representative, homogenized) slag from anode furnace 09TT05247
Constituent 1
Results and discussion
- Results:
- The tested materials were characterized (physico-chemical and mineralogical properties) in view of the upcoming REACH registrations of copper intermediates and copper slags by the Copper Consortium.
Any other information on results incl. tables
The studied four (4) slag samples from copper refining contain 1- 38% copper, 16.1- 40.3% iron, 0.01- 3.1% nickel, 0.4- 11.2% lead, 0.01- 8.8% tin, 0.8- 3.5% zinc, 12.5- 32% SiO2 and 0.05- 5.6% sulphur. As they vary in chemical composition, also the mineral composition varies between different samples.
Sample 09TT03335 consist mainly of amorphous glass (24.8%), metallic copper (12.7%), stannopalladinite –type copper –tin compound and lead –bearing amorphous glass (11.6%). Sample 09TT03987 consist mainly of fayalite (30.6%), magnetite (22.4%), chalcocite (17.7%) and amorphous glass (15.7%). Sample 09TT05247 consist mainly of delafossite (27.6%), magnetite (22.4%), cuprite (20.8%) and amorphous glass (20%) and the last sample 09TT05248 consist mainly of fayalite (61.1%) and amorphous glass (28.8%).
The chemical analysis of studied sampled are given in Table 7 and Table 8 and their mineralogical composition in Table 9 and Table 10 with distribution of copper.
Table7: Chemical composition of studied sample, part 1
Lab code |
|
|
09TT03335 |
09TT03987 |
09TT05247 |
09TT05248 |
Sample code |
|
|
B8 |
B8 |
B8 |
B8 |
|
|
|
|
|
|
|
Cu |
P1 |
% |
< 0.004 |
<0.005 |
0.02 |
<0.005 |
|
P2 |
% |
4.15 |
1.78 |
18.10 |
0.31 |
|
P3 |
% |
7.32 |
16.00 |
11.40 |
0.40 |
|
P4 |
% |
7.32 |
1.50 |
6.04 |
0.16 |
|
Sum |
|
18.79 |
19.28 |
35.56 |
0.87 |
|
TOT |
% |
21.80 |
19.80 |
38.00 |
0.99 |
|
|
|
|
|
|
|
As |
P1 |
% |
< 0.004 |
<0.005 |
<0.005 |
<0.005 |
|
P2 |
% |
< 0.010 |
0.04 |
<0.011 |
0.03 |
|
P3 |
% |
< 0.02 |
0.03 |
<0.005 |
0.01 |
|
P4 |
% |
< 0.002 |
0.11 |
0.01 |
0.01 |
|
Sum |
|
0.00 |
0.17 |
0.01 |
0.05 |
|
TOT |
% |
0.06 |
0.23 |
0.07 |
0.06 |
|
|
|
|
|
|
|
Fe |
P1 |
% |
< 0.004 |
<0.005 |
<0.005 |
<0.005 |
|
P2 |
% |
9.27 |
14.20 |
6.62 |
18.80 |
|
P3 |
% |
0.07 |
1.11 |
0.05 |
0.12 |
|
P4 |
% |
2.66 |
7.29 |
2.70 |
12.30 |
|
Sum |
|
12.00 |
22.60 |
9.37 |
31.22 |
|
TOT |
% |
16.10 |
36.70 |
21.40 |
40.30 |
|
|
|
|
|
|
|
Ni |
P1 |
% |
< 0.004 |
<0.005 |
<0.005 |
<0.005 |
|
P2 |
% |
0.14 |
<0.014 |
0.20 |
0.02 |
|
P3 |
% |
0.04 |
0.01 |
0.01 |
<0.005 |
|
P4 |
% |
1.23 |
0.01 |
0.13 |
0.02 |
|
Sum |
|
1.41 |
0.01 |
0.34 |
0.04 |
|
TOT |
% |
3.06 |
0.01 |
2.06 |
0.06 |
|
|
|
|
|
|
|
Pb |
P1 |
% |
0.12 |
<0.005 |
<0.005 |
<0.005 |
|
P2 |
% |
0.22 |
0.09 |
0.12 |
0.07 |
|
P3 |
% |
0.10 |
0.05 |
0.01 |
0.01 |
|
P4 |
% |
8.85 |
0.35 |
0.53 |
0.17 |
|
Sum |
|
9.29 |
0.48 |
0.67 |
0.25 |
|
TOT |
% |
11.30 |
0.55 |
3.76 |
0.40 |
|
|
|
|
|
|
|
P1= H2O, P2= H2SO4, P3= KCN+Br-MeOH, P4= HNO3–soluble, TOT= total -, BM= bromine-methanol dissolutions, KEM= ion exchange chromatography, LECO = S/C analyzer, satmagan = Fe3O4analyzer, n.a. = not analyzed
Table 8: Chemical composition of studied sample, part 2
Lab code |
|
|
09TT03335 |
09TT03987 |
09TT05247 |
09TT05248 |
Sample code |
|
|
B8 |
B8 |
B8 |
B8 |
|
|
|
|
|
|
|
Co |
TOT |
% |
0.32 |
0.03 |
0.09 |
0.02 |
Sb |
TOT |
% |
0.43 |
0.06 |
0.06 |
0.03 |
Sn |
TOT |
% |
8.82 |
0.01 |
0.36 |
0.12 |
Zn |
TOT |
% |
3.45 |
0.75 |
2.08 |
1.99 |
Mo |
TOT |
% |
0.01 |
n.a. |
n.a. |
n.a. |
Ag |
TOT |
% |
0.01 |
0.00 |
<0.010 |
<0.010 |
|
|
|
|
|
|
|
Se |
TOT |
% |
< 0.003 |
<0.006 |
n.a. |
n.a. |
Sr |
TOT |
% |
0.01 |
n.a. |
n.a. |
n.a. |
Te |
TOT |
% |
< 0.002 |
<0.006 |
n.a. |
n.a. |
Cd |
TOT |
% |
n.a. |
0.01 |
n.a. |
n.a. |
|
|
|
|
|
|
|
SiO2 |
KEM |
% |
20.50 |
17.70 |
12.50 |
32.00 |
Al2O3 |
TOT |
% |
2.51 |
2.23 |
1.01 |
2.96 |
Cr2O3 |
TOT |
% |
0.42 |
0.05 |
0.07 |
0.05 |
K2O |
TOT |
% |
0.06 |
0.06 |
0.20 |
0.74 |
MgO |
TOT |
% |
0.39 |
0.50 |
0.60 |
0.74 |
MnO |
TOT |
% |
0.17 |
0.02 |
0.03 |
0.05 |
Na2O |
TOT |
% |
0.35 |
0.25 |
6.97 |
0.39 |
CaO |
TOT |
% |
3.07 |
1.57 |
0.51 |
2.06 |
TiO2 |
TOT |
% |
0.04 |
n.a. |
n.a. |
n.a. |
Ba |
TOT |
% |
0.02 |
0.04 |
n.a. |
n.a. |
|
|
|
|
|
|
|
B |
TOT |
% |
0.07 |
n.a. |
n.a. |
n.a. |
S |
Leco |
% |
0.08 |
5.60 |
0.05 |
0.58 |
SO42- |
KEM |
% |
n.a. |
0.06 |
<0.025 |
<0.025 |
C |
Leco |
% |
0.07 |
0.08 |
0.07 |
0.08 |
Satmagan |
|
% |
5.43 |
22.40 |
22.40 |
7.16 |
|
|
|
|
|
|
|
Surface area |
|
m2/g |
0.4 |
1.97 |
0.13 |
0.06 |
Density |
|
g/cm3 |
5.04 |
5.57 |
4.8 |
3.8 |
|
|
|
|
|
|
|
P1= H2O , P2= H2SO4, P3= KCN+Br-MeOH, P4= HNO3–soluble, TOT= total -, BM= bromine-methanol dissolutions, KEM= ion exchange chromatography, LECO = S/C analyzer, satmagan = Fe3O4analyzer, n.a. = not analyzed
Applicant's summary and conclusion
- Conclusions:
- good quality study that assessed full chemistry and mineralogy of several representative Copper rich-slags. A RWC mineralogy can be derived for each specific slag (distribution pattern for each key element, i.e. % from Total into the various mineralogical forms/species present into the UVCB). They can be used for classification of the UVCB substance (mixture toxicity rules)
- Executive summary:
The chemistry and mineralogy of Slag, copper refining B8 intermediate was assessed by Liippo et al, 2010 . In this assessment, samples of slags, corresponding to different types of materials were characterized. Samples were selected as representative for the production processes, depending on origin of the raw material (primary or secondary smelter). Sampling and sample preparation was performed according to the “ECI sampling protocol REACH B8” (see IUCLID Section 1.4 Analytical information):
Type I: slag concentrate, from concentrator (primary smelter)
Type II: slag from FSF flash furnace, primary smelter
Type III: slag from anode furnace, primary smelter
Type IV: slag from recycler, secondary smelter
The studied four (4) slag samples from copper refining contain 1- 38% copper, 16.1- 40.3% iron, 0.01- 3.1% nickel, 0.4- 11.2% lead, 0.01- 8.8% tin, 0.8- 3.5% zinc, 12.5- 32% SiO2 and 0.05- 5.6% sulphur. As they vary in chemical composition, also the mineral composition varies between different samples.
Sample 09TT03335 (type IV secondary smelter) consist mainly of amorphous glass (24.8%), metallic copper (12.7%), stannopalladinite –type copper –tin compound and lead –bearing amorphous glass (11.6%). Sample 09TT03987 (type I concentrator) consist mainly of fayalite (30.6%), magnetite (22.4%), chalcocite (17.7%) and amorphous glass (15.7%). Sample 09TT05247 (type III anode furnace) consist mainly of delafossite (27.6%), magnetite (22.4%), cuprite (20.8%) and amorphous glass (20%) and the last sample 09TT05248 (type II flash furnace/primary smelting) consist mainly of fayalite (61.1%) and amorphous glass (28.8%).
The chemistry and mineralogical data demonstrated that all tested slags correspond to the identity described above, although the mineralogical composition of the UVCB may vary slightly (see composition IUCLID Section 1.2). Slags from copper refining are made mainly of various glass, fayalite and/or magnetite, with largely varying amounts of elements such as Cu, Ni, Pb, etc. Depending on the process, these elements are mainly in the forms of sulphides + alloy/metal inclusions (e.g. slags from primary smelters), or mainly in the forms of oxides + alloy/metal inclusions (e.g. slags from converter and refining slags).
For each type of slag, characteristic distribution patterns for each constituting element were observed:
Type I: Representative slag was from concentrator (Sample code 09TT03987)
Copper is in the form of metal/inclusion (WC powder, 2.58% from total CU) + sulphides (88.43% from total Cu)+ oxides (8.99% from total Cu)
Lead in the form of Pb compounds (20% from total Pb)+ metal (WC powder, 80% from total Pb)
Nickel is in the form of metal/inclusion (WC powder, 100% from total Ni)
Zinc is in the form of sulphides (100% from total Zn)
Arsenic is in the form of alloy/inclusions (100% from total As)
Antimony is in the form of alloy/inclusion (100% from total Sb)
other metal elements: same distribution pattern than copper (WC)
Type II: Representative slag was from FSF primary smelter (sample code 09TT05248)
Copper is in the form of metal/inclusion (WC powder, 61.47% from total CU) + sulphides (38.52% from total Cu)
Lead in the form of Pb compounds (100% from total Pb)
Nickel is in the form of metal (WC powder, 50% from total Ni) + sulphides (50% from total Ni)
Zinc is in the form of metal (WC powder, 77.4% from total Zn) + sulphides (22.6% from total Zn)
Arsenic is in the form of alloy/inclusions (100% from total As)
Antimony is in the form of alloy/inclusion (100% from total Sb)
other metal elements: same distribution pattern than copper (WC)
Type III: Representative slag was from Anode furnace (Sample code 09TT05247)
Copper is in the form of metal/inclusion (WC powder, 61.5% from total CU) + oxides (38.5% from total Cu)
Lead in the form of Pb compounds (78.94% from total Pb) + metal (21.06% from total Pb)
Nickel is in the form of metal (WC powder, 61.50% from total Ni) + oxides (38.50% from total Ni)
Zinc is in the form of metal/inclusion in silicates (WC powder, 100% from total Zn)
Arsenic is in the form of alloy/inclusions (100% from total As) other metal elements: same distribution pattern than copper (WC)
Type IV: Representative slag was from Secondary smelter(Sample code 09TT03335)
Copper is in the form of metal/inclusion (WC powder, 74.21% from total CU) + oxides (25.79% from total Cu)
Lead in the form of Pb compounds (57% from total Pb) + metal (43% from total Pb)
Nickel is in the form of metal (WC powder, 67.12% from total Ni) + oxides (32.88% from total Ni)
Zinc is in the form of oxides (100% from total Zn)
Arsenic is in the form of alloy/inclusions (100% from total As)
Antimony is in the form of oxides (100% from total Sb) other metal elements: same distribution pattern than copper (WC)
For classification purposes, the two following Reasonable Worst Case (RWC) scenarios were retained:
RWC Sulphide scenario (applicable to major (primary) smelting and slags from concentrator):
Copper is in the form of metal/inclusion (WC powder, 2.58% from total CU) + sulphides (88.43% from total Cu)+ oxides (8.99% from total Cu)
Lead in the form of Pb compounds (WC, 100% from total Pb)
Nickel is in the form of sulphides (WC, 100% from total Ni)
Zinc is in the form of sulphides (WC, 100% from total Zn) Arsenic is in the form of alloy/inclusions (100% from total As)
Antimony is in the form of alloy/inclusion (100% from total Sb)
other metal elements: same distribution pattern than copper (WC)
RWC Oxide scenario (applicable to (primary and secondary) converting and refining slags):
Copper is in the form of metal/inclusion (WC powder, 61.5% from total CU) + oxides (38.5% from total Cu)
Lead in the form of Pb compounds (WC, 100% from total Pb)
Nickel is in the form of oxides (WC, 100% from total Ni)
Zinc is in the form of metal/inclusion in silicates (WC powder, 100% from total Zn)
Arsenic is in the form of alloy/inclusions (100% from total As)
other metal elements: same distribution pattern than copper (WC)
The above distributions patterns are conservative, in particular in respect to Pb (assuming Pb is either soluble compound form or partially soluble powder form) and to Nickel (assuming Ni is always in soluble compound forms). Considering the chemical compositions across industry, two grades for each of the above scenarios were derived in order to cover the worst cases for key drivers of classifications.
Information on Registered Substances comes from registration dossiers which have been assigned a registration number. The assignment of a registration number does however not guarantee that the information in the dossier is correct or that the dossier is compliant with Regulation (EC) No 1907/2006 (the REACH Regulation). This information has not been reviewed or verified by the Agency or any other authority. The content is subject to change without prior notice.
Reproduction or further distribution of this information may be subject to copyright protection. Use of the information without obtaining the permission from the owner(s) of the respective information might violate the rights of the owner.
